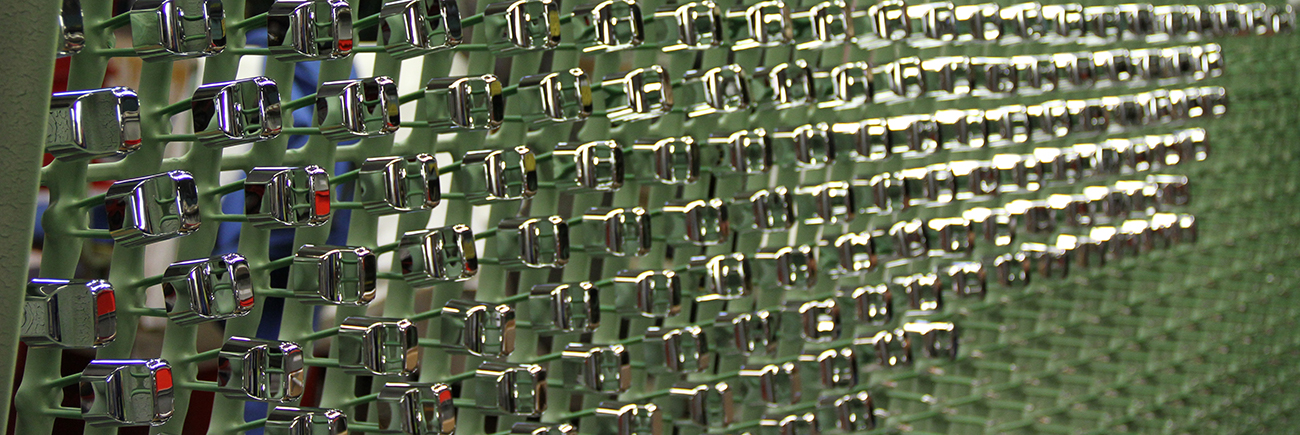
Harkosta hanaksi: näin valmistuu Oras-hana
Oras-hanan valmistaminen on monivaiheinen prosessi, josta suuri osa on käsityötä. Laatua valvotaan valmistuksen joka käänteessä. Kävimme maajohtaja Marko Sundholmin kanssa tutustumiskierroksella Oraksen Rauman tehtaalla, jossa valmistuu noin 3 000 hanaa päivässä.
Oras-hanojen valmistaminen on osin automatisoitua mutta edelleen käsityövaltaista. Hanan valmistuksen vaiheet ovat tiivistetysti keernan valmistus, valu, sahaus, koneistus, hionta, kiillotus, kromaus, kokoonpano ja testaus. Ennen tätä kaikkea on kuitenkin tehty jo paljon työtä: uusi tuote on suunniteltu ja valmistusta simuloitu tietokoneella, minkä jälkeen on tehty koevaluja ja hienosäätöjä niin kauan, että valu on onnistunut täydellisesti. Valussa tarvittavat työkalut, valukokillit ja keernalaatikot valmistetaan Oraksella itse.
Valu alkaa messinkiharkosta ja keernasta
Hanavalmistuksen tärkein raaka-aine on messinki, josta hanarunko valmistetaan valamalla. Keerna on keskeinen osa hanan valmistusta, sillä se muodostaa valun aikana hanarungon vesikanavat. Keerna valmistetaan hienojakoisesta hiekasta ja kovettimesta yhtenäiseksi kappaleeksi keernalaatikossa kuumentamalla.
Tehtaan valimoon toimitetaan kuormalavoittain messinkiharkkoja. Harkot ovat sinkinkadon kestävää erikoismessinkiä.
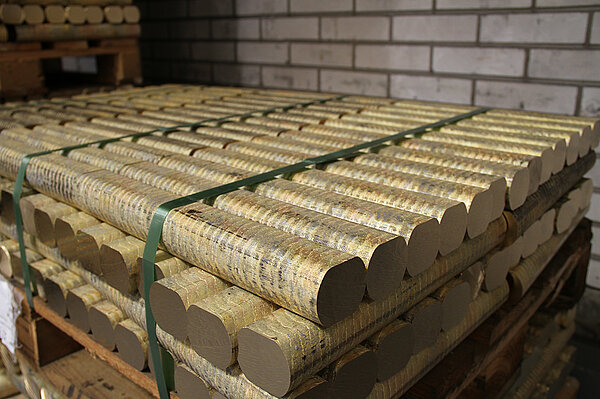
”Toisin kuin esimerkiksi Keski-Euroopassa, Pohjoismaissa vesijohtovesi on hapanta ja syövyttää putkia – vaikka se on turvallista käyttää talousvetenä, se on kemiallisesti aggressiivista. Siksi tavallinen messinki ei kelpaa meille”, kertoo Oraksen Suomen maajohtaja Marko Sundholm.Valussa valukokilli kastetaan vesi-grafiittiliuokseen. Valuri asettaa keernat muottiin ja puhdistaa paineilmalla valukokillin mahdollisesta irtohiekasta.
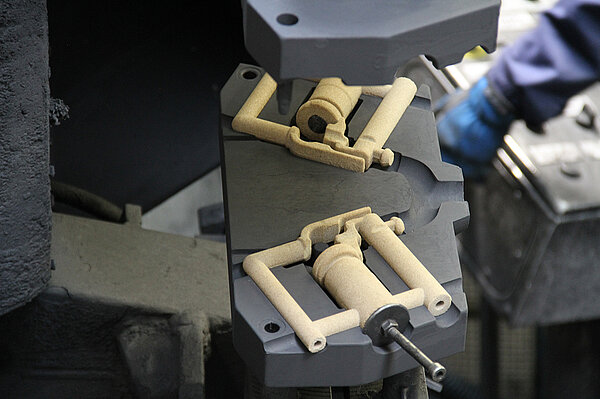
Muotti suljetaan, ja se kääntyy valu-uunin hehkuvan kuuman valupään päälle. Kolme tonnia sulaa messinkiä sisältävästä valu-uunista sula messinki siirtyy valukokilliin. Keerna pitää muotin sisällä avoinna ne osat, joihin asennetaan tekniikkaa ja joita pitkin vesi kulkee hanan läpi.
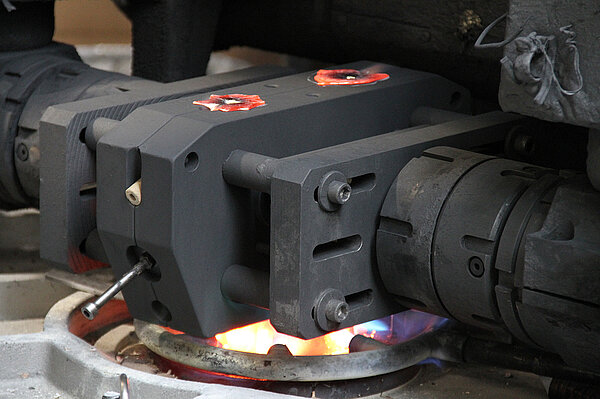
Nopean jäähdytyksen jälkeen valaja siirtää valoksen pihdeillä käsin jäähtymään. Tämän jälkeen keerna poistetaan hanarungon sisältä pyörittämällä sitä metallikuulin varustetussa myllyssä.
Hana sahataan ja hiotaan lopulliseen muotoonsa
Valimosta tulleet, jäähtyneet hana-aihiot sahataan irti toisistaan ja niistä poistetaan osat, jotka olivat valun onnistumisen kannalta tärkeitä mutta jotka eivät kuulu valmiiseen hanaan. Sahaus tehdään Oraksella sekä automatisoidusti että käsityönä.
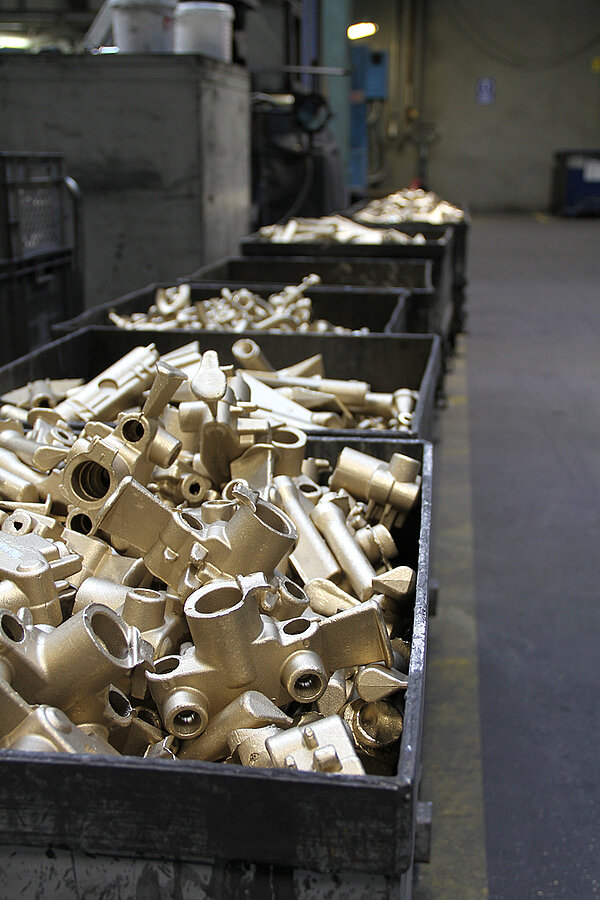
”Työvaihetta on automatisoitu, mutta joidenkin kappaleiden vaativuuden takia automatisointi on hankalaa”, sanoo Marko Sundholm.
Hana-aihio siirretään seuraavaksi liukuhihnalle, joka kuljettaa sen läpi automatisoitujen koneistus-, hionta- ja kiillotusprosessien. Valmistuksen alkuvaiheissa syntynyt karkea pinta hiotaan monivaiheisessa prosessissa pois. Hionnan jäljiltä uurteinen metallipinta kiillotetaan virheettömäksi. Lopuksi työntekijät tarkistavat laadun omin käsin ja silmin. Pienet erikoistuote-erät saatetaan hioa ja kiillottaa käsin. Myös korjauksia voidaan tehdä käsinkiillotuksena.
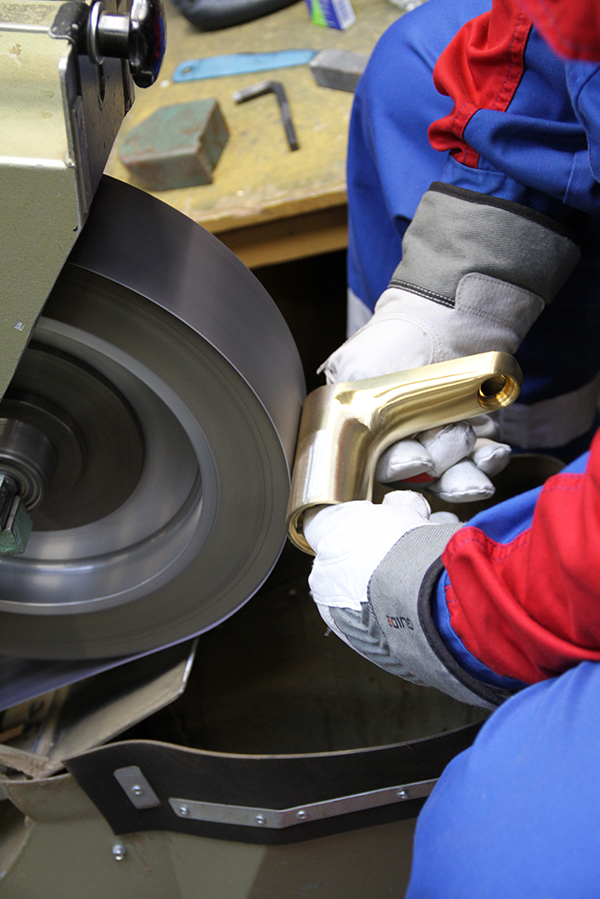
”Sahauksessa ja koneistuksessa yli jäävä jätemessinki ei suinkaan mene hukkaan, vaan arvokas raaka-aine kerätään talteen. Sahausjätteet sulatetaan valu-uunissa ja valetaan uudestaan. Koneistuslastut toimitetaan takaisin harkkojen toimittajalle, joka käyttää ne hyödyksi uusien harkkojen valmistuksessa. Uutta messinkiä on harkoissa hyvin vähän”, kertoo Sundholm.
Kromipinnoite ei salli virheitä
Lopuksi hanat pinnoitetaan kromilla. Kromi tekee hanan pinnasta kovan, kiiltävän ja kulutusta kestävän.
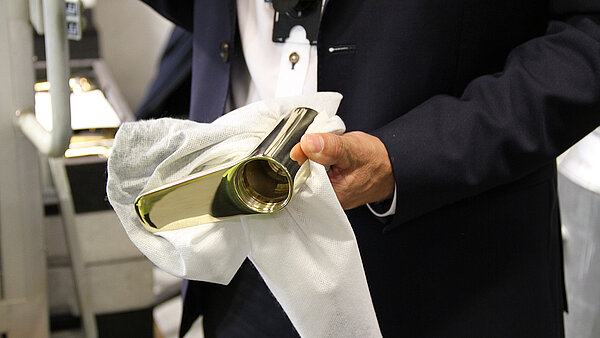
”Tuotteiden pintojen on oltava ennen kromausta virheettömiä, sillä kromi on armoton pintamateriaali. Se ei peitä vaan päinvastoin korostaa pieniäkin virheitä”, Sundholm sanoo. Myös hanan muovista tai komposiittimateriaalista valmistetut näkyville jäävät osat kromataan. Muovi- ja komposiittiosia tehdään Oraksen omassa puristamossa.
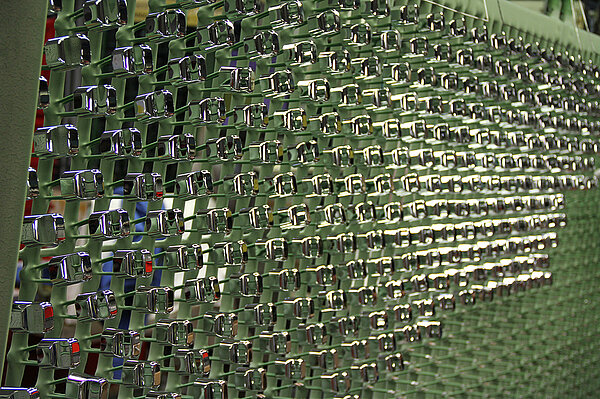
Muovin kromaaminen on messingin kromaamista haastavampaa: ”Muovista on tehtävä sähköä johtavaa, jotta kromaus on mahdollista: muoviosa päällystetään kuparikerroksella ja sen jälkeen nikkelikerroksella, jolloin pinnoitteen alle muodostuu lämpölaajenemiselta suojaava jousituskerros”, Sundholm selittää.
Kromaus vie noin kaksi tuntia, joiden aikana tuote käy erilaisissa pinnoitekylvyissä ja pesuissa noin 40 kertaa. Kromauksen jälkeen tuotteet tarkastetaan ennen kuin osat lähtevät kokoonpanoon. Mahdolliset merkinnät, kuten esimerkiksi tuotemerkki, tehdään tässä vaiheessa. Merkkaus tehdään nykyään pääsääntöisesti laseroimalla.
Hanan sisälle asennetaan tekniikkaa
Oras valmistaa itse hanojen sisälle asennettavia komponentteja, jotka esimerkiksi säätelevät veden virtausta ja lämpötilaa.
”Vipuhanan sielu on komponentti nimeltä säätöosa, ja se on ollut kaikissa Oraksen malleissa samanlainen jo vuodesta 1982. Säätöosan avulla hallitaan veden virtaamaa ja lämpötilaa, jotta hanasta saadaan halutunlämpöistä vettä toivottu määrä. Säätöosat valmistetaan Raumalla. Jokainen kappale merkitään, ja siksi osat ovat jäljitettävissä”, Marko Sundholm kertoo.
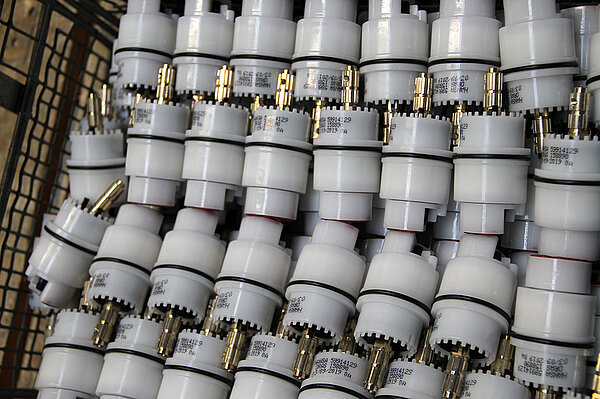
Hanan suunnittelussa tulee ottaa huomioon monia eri määräyksiä ja standardeja. Tuotekehityksen aikaa vievin osa onkin Sundholmin mukaan saada hanan ääni riittävän hiljaiseksi. ”Hanan ääniluokka testataan erillisessä laboratoriossa, kelluvarakenteisessa betonisessa huoneessa, jossa on täysin hiljaista,” hän sanoo.
Hanan sisälle tulevat komponentit ja etenkin edistyneissä vesikalusteissa tärkeässä osassa oleva elektroniikka asennetaan hanan sisälle kokoonpanossa. Oras-hanojen kokoonpanoa suoritetaan sekä käsin, että automaattilinjoilla, mutta lopputarkastuksen tekee ja laatua valvoo aina ihminen.
”Rauman tehtaalta valmistuu keskimäärin 3 000 hanaa päivässä. Valmiista hanoista yksi prosentti tarkastetaan vielä kerran pistokokein. Lopuksi hana pakataan myyntipakkaukseen, ja se on valmis lähtemään maailmalle”, Sundholm kertoo.
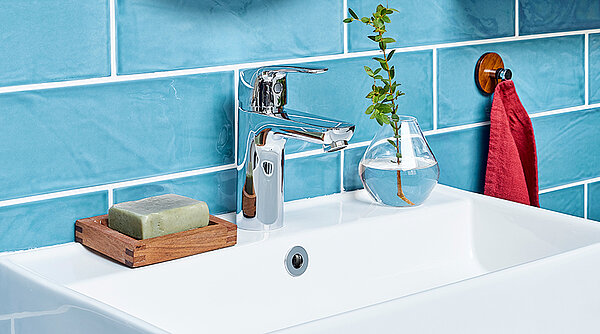
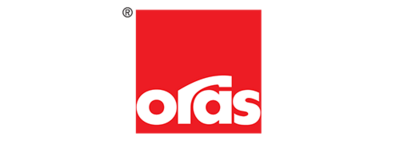
Dahlin tuotevalikoiman Oras Safira -hanat
Teksti ja kuvat on julkaistu alunperin Oraksen blogissa https://stories.oras.com/fi/harkosta-hanaksi-n%C3%A4in-valmistuu-oras-hana